The filter bag is a key accessory that determines the dust removal efficiency and working temperature of the bag filter. The cost of replacing the filter bag is also the main maintenance cost of the bag filter. Therefore, the working life of the filter bag is related to the operation status and cost of the filter. The filter material and the reasonable design of the structure are particularly important.
The selection of filter material should be based on the temperature, humidity and chemical characteristics of the gas; the size, weight, shape of the particulate material, whether it is pecking abrasive or not, as well as the dust concentration, filtration speed, cleaning method, emission concentration and the work of the bag filter System and other factors are considered comprehensively. In general, needle-punched felt is used for pulse-blown bag filter, and woven fabric is used for sub-chamber back-blowing bag filter or mechanical vibrating bag filter.
1. Matters needing attention in filter bag processing
After selecting the shape of the filter material used in the filter bag and determining the specifications of the filter bag, the following matters should be paid attention to during the processing.
①Accurately design the size of the filter cloth required for each part of the filter bag, and the actual amount of the filter cloth is larger than the designed size, leaving room for it.
② Correctly select the accessories of the required filter bag, determine its specifications and check its quality; the accessories of the filter bag should match the quality requirements of the filter bag.
③ The filter bag should be marked, cut, cut and sewn on the automatic production line. When the filter bag is manually processed, it should be unfolded on the operating platform, and a certain pulling force should be applied to keep it flat.
④The processing process shall strictly implement the quality standards, and proceed according to the design drawings and operating techniques. Operators should wear work clothes and shoes and hats that meet the requirements, and smoking is strictly prohibited.
⑤ The operator should be responsible for the products processed by himself based on the principle of quality first and reputation first, and inspect them one by one to eliminate waste, disabled and defective products at the source.
2. Sewing of filter bags
In general, the suture material of the filter bag should be the same as that of the filter material. In special cases, when a suture of a material different from the filter material is used, the strength, heat resistance and chemical resistance of the suture should be superior to those of the same material as the filter material.
The number of suture lines of the filter bag. The longitudinal stitching of the filter bag body must be firm and straight, and not less than 3. The bottom and the mouth of the bag can be sewn with single needle or double needle according to different requirements. The needle density of the filter bag sewing is related to the material of the filter bag. It ensures the tightness and sewing strength of the sewing place without leakage of dust and does not damage the strength of the filter cloth itself. The needle density of the chemical fiber filter cloth filter bag should be within 10cm (25±5); the needle density of the glass fiber filter cloth filter bag should not be too large. The sewing width of the dust filter bag is related to the material of the filter material, generally 9-12cm. The distance between the outer sewing needle and the edge of the filter cloth; the needle felt is 2-3mm, and the glass fiber filter material is 5-8mm.
After the filter bag is sewn, it should be inspected and repaired according to the design requirements to eliminate creases, oil stains and grease on the surface. For filter bags sewed with film-coated filter cloth, in addition to strict requirements on the needle size used, the control of needle density and operating procedures, all needle holes should be repaired with special materials.
3. Inspection of filter bags
Filter bag manufacturers should be based on national standards, industry standards, and corporate standards. The quality supervision department of the factory selects items by batch and the proportion of sampling. Generally, the sampling inspection ratio of filter bags by batch is 5% to 20%, and the sampling inspection ratio of filter bags with higher requirements should be more than 15%.
Ex-factory products shall be subject to strict ex-factory inspection according to the requirements of the order contract for processing filter cloths, sutures and various accessories of filter bags. Problems found should be corrected before leaving the factory.
For filter bags that are resistant to temperature, acid and alkali corrosion, and anti-static, special inspections are required.
4. Packaging and storage of filter bags
①Packaging of filter bags. Different types of filter bags must be packaged separately. Generally, it is better to use plastic bags for each filter bag, and several filter bags are packed in a carton. The filter bags must be neatly arranged and packed regularly. For filter bags with anti-shrinkage rings, the ring should be prevented from being deformed under pressure; for filter bags that need to maintain their shape (such as glass fiber needled felt filter bags), it is necessary to use bag fillers. , boxed and packaged.
②Filter bag logo. There should be printed signs on the outside of the packing box (or packing bag), including the name of the factory, the name of the product, the model, the specification, the quality grade and the date of manufacture.
③Storage and transportation. The product should be stored in a ventilated and dry area at room temperature that is not exposed to sunlight. The distance from the ground and the wall should not be less than 300mm. Sufficient (>700-1000mm) passages should be reserved between the stacks of each batch of products. high temperature objects. A sufficient number of fire-fighting equipment should be stored in the warehouse according to fire protection requirements and should be regularly inspected. During the transportation of the product, it is necessary to prevent rain and water contamination.
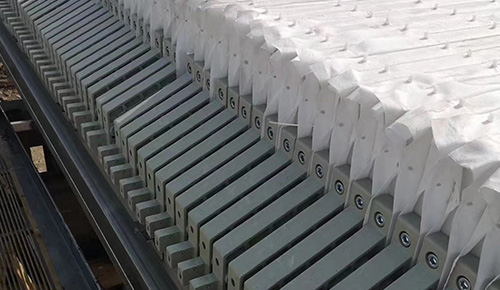
No comment