Power Industry
In order to ensure that the project meets the 10mg emission requirements, the company uses independently developed and designed high-precision filter materials to make filter bags, which can ensure that the ultra-low emission requirements can be met; at the same time, the company arranges technical experts in various aspects such as project installation, testing, and protection. Fine management of the whole process.
PPS+PTFE dust bag:
Features:
The base fabric and the front/back surface are all 100% PPS material;
PTFE+PPS is composed of front/back dust surface, which greatly improves chemical performance and is suitable for highly corrosive working conditions; it is composed of PTFE base cloth + PPS front/back dust surface in the middle to improve chemical resistance, usually in coal containing Slightly higher sulfur content.
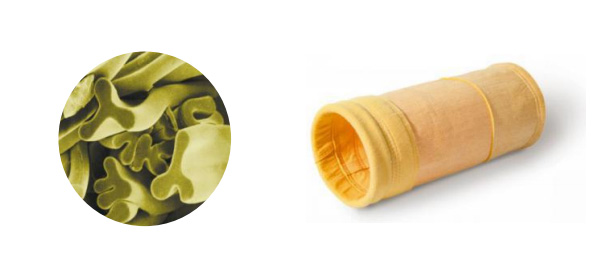
Applicable working conditions:
Especially suitable for processes with high emission concentration requirements
Flue gas purification for cement, kiln, drying, combustion, smelting, asphalt mixing;
Flue gas purification of various industrial kilns and coal-fired boilers;
Partial waste incineration flue gas purification, etc.;
PTF E – PTFE Dust Bag:
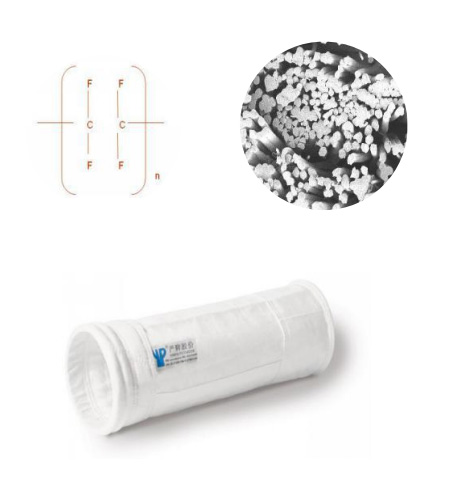
Features:
Under the continuous operation of 240 ℃ and the instantaneous temperature of 260 ℃, it can resist acid and alkali erosion in the entire pH value range; therefore, it is often blended with other materials to improve the chemical resistance of the filter material;
Applicable working conditions:
Suitable for harsh conditions requiring corrosion resistance and occasions with high filter life requirements
Waste incineration, carbon black production, titanium dioxide (Ti O 2 ) production process;
The primary smelting, refining and chemical production process of some metals;